When a Colorado family recently moved into their brand-new multi-family home near Denver, they were excited to finally be free of worry about the indoor air quality that had plagued each of them in other buildings all their lives. Kyle, a medical doctor, his wife Linda (names have been changed for privacy), and their two children all carry a combination of the genes that, when exposed to mold, make them more susceptible to developing Chronic Inflammatory Response Syndrome (CIRS).
Kyle and his family had done their homework; they had purchased a newly constructed townhome—one that they had every reason to assume was free of mold or water damage that they might react to. However, just to be certain, they had their living space tested before moving in. Disappointingly, the tests showed high levels of water-damage mold.
What the testing confirmed is likely happening with new construction across the country: raw materials such as wood, drywall, or plywood are delivered to the site with mold built in. This is especially common with wood and plywood, which may be exposed to the elements for months before they are enclosed under a protective roof. During that time, rain or snow can soak these materials and allow mold to grow. In the case of this family’s home, the drywall was installed incorrectly—in contact with the concrete slab, where it freely wicked up moisture as the concrete dried. Ultimately, the backside of all the drywall was found to be covered in mold, and a mitigation company had to remove the lower half of the drywall throughout the house and reinstall it with the recommended half-inch of separation from the slab.
Any of us would be excused for assuming brand-new multi-family homes, such as apartments, condos, and hotels would be mold-free. Though that’s a fair assumption, it may very likely be untrue. Unfortunately, current building codes don’t protect the health of the individuals when it comes to mold. Local building departments, along with developers and contractors, sincerely want to build a sound product, but this dilemma is most often unchecked.
There are three primary reasons mold grows in brand-new multi-family housing:
1. Precipitation – The process of building takes a long time—usually months, especially for multiple-floor buildings. Since the time to seal the structure against the elements is so lengthy, it really doesn’t matter whether it is being constructed in a typically wet or dry climate because materials such as drywall or Oriented Strand Board (OSB) can absorb moisture and grow dangerous mold. In addition, today’s architectural trend of the modern look means many structures have flat roofs, which causes water to find its way between the sheets of roofing plywood and further leads to pooling on each floor below. This sets up a predictable standing water problem and the potential for mold growth. Mold needs oxygen, water, and organic material to grow, and that growth begins within as few as 24-48 hours.
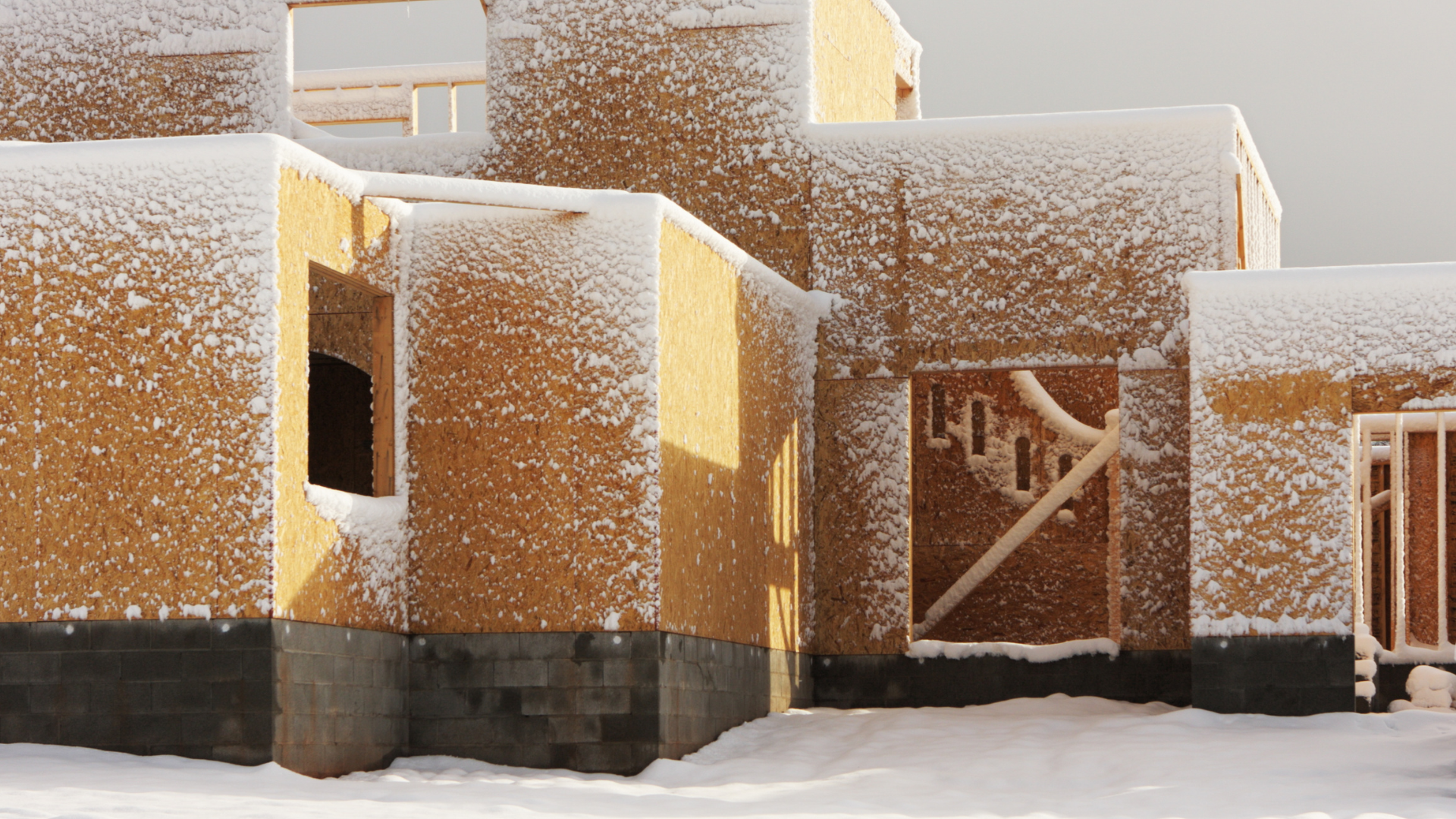
2. Concrete/Drywall – These materials are great sponges. Most people think of concrete as a hard surface that repels water. However, to a large extent, that is not correct. In fact, all concrete is porous, and water is part of every concrete mixture. Unless the concrete is sealed, which can make it quite slippery depending on the texture, concrete will absorb water until its saturation point. To put that in perspective, normal density concrete has an absorption rate of 10% to 15% (What is water absorption test of concrete? Explain in detail with test procedure and examples, n.d.). Where does that moisture go? The short answer is that it takes a long time to dry out. During this time period, water can be absorbed out of the concrete into other adjacent porous materials, such as wood. In a framed wall, the bottom piece of wood, typically referred to as the bottom plate, is required by building code to be treated in order to hinder microbial growth. However, the biggest sponge is often drywall. Drywall companies are supposed to hang the bottom piece 1/2” to 3/4” above the floor. If, instead, the drywall is touching the concrete anywhere, water within the concrete will be absorbed into the drywall, and more importantly, the paper facing. According to testing, mold spores have been proven to already be embedded within the paper of the drywall immediately after being manufactured—even before it is shipped to the build site. These molds include Aspergillus, Chaetomium, and Stachybotrys chartarum. These mold spores stay encapsulated within the drywall paper until it gets wet, either from rain, snow, or contact with concrete. At this point, the mold begins to grow and the problems multiply (How Does Mold on Drywall in New Construction Happen? n.d.).
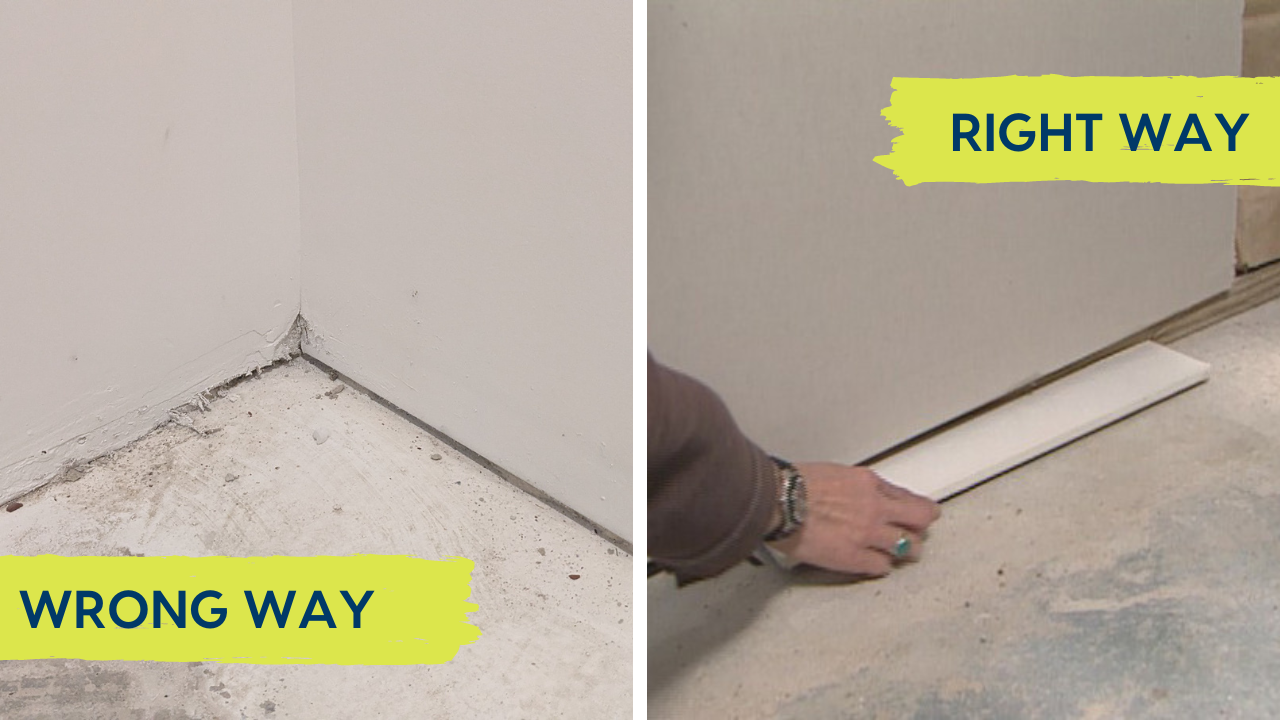
3. Oriented Strand Board (OSB) – This is the predominant type of wood panel used in most structures built today. There are all sorts of scientific reasons that mold grows on OSB more than on multi-layered plywood and other products, and you can read the referenced document below if you want to geek out. In summary, OSB is extremely prone to mold growth, which presents an overwhelming challenge since OSB is used in practically every multifamily structure in the United States. The OSB sits under the elements—rain and snow—often for weeks or months, rather than drying in the sunshine as soon as the next floor is built. Precipitation soaks the current top floor, then finds its way between the OSB joints and drips down to the next floor and the next, creating a high-growth mold box (Lstiburek, 2009).
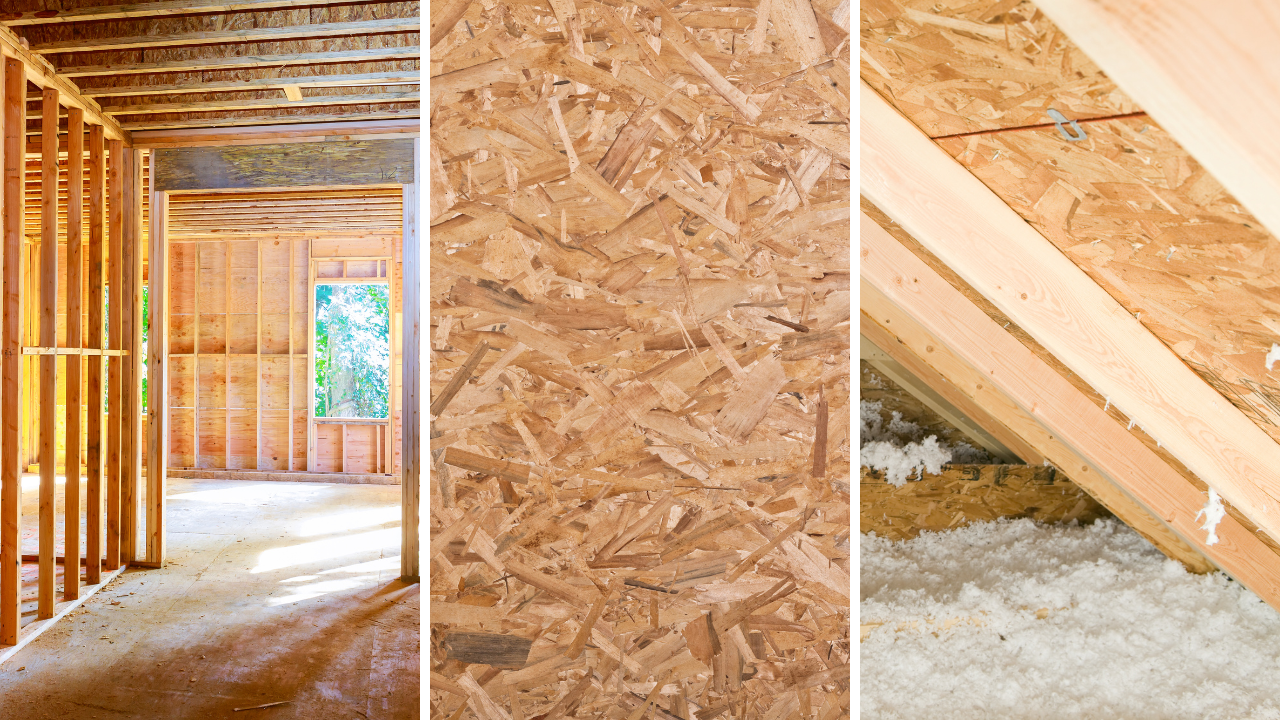
These scenarios can render a brand-new apartment building mold-ridden and unlivable for people highly sensitive to microbial growth and mycotoxins. They believe they are safe because they assume “new” means “safe”. It’s also very difficult to detect mold odor in a new building due to the natural off-gassing of the materials used to build it. This problem is wreaking havoc on the air quality of multi-family buildings and custom homes for people with mold allergies or mold illness.
As the president of Tinker Homes, I have spent the past 20 years building new custom homes. Although I prefer to frame these structures during the winter (snow is easy to shovel off the OSB and drywall to remove the moisture), I’m also very careful to build as quickly as possible during the framing stage so we can “dry-in” the home before water and mold damage can occur. “Dried-in” refers to a building that has roofing paper, an exterior vapor barrier, and windows installed. How can a homebuyer know which structures are safe or not? It’s a difficult question to answer. I wish I could assure you that all OSB and drywall are perfectly safe when they arrive at the building site and that the contractors building these structures are careful, ensuring mold growth doesn’t occur. I would love to tell you that the entire structure was cleaned in a way to ensure maximum health for its future occupants. However, this simply is not our reality.
It’s possible that the people now occupying these structures could be living in the presence of water-damage mold and, depending on their genetic makeup, may be suffering tremendously without knowing why.
A much better option would be a multifamily structure built with concrete floors on each level, but those are hard to find because that type of construction is much higher in cost. Ultimately, people are better off finding a small complex of four to six units that was dried-in quickly during construction.
As for the concrete and drywall, people are faced with having to place their trust in contractors. I’m one of them, and I don’t like criticizing other contractors, but most of them are simply not educated on the various practices surrounding healthy home construction. In addition, they are understandably concerned with the building timeline and the bottom line, but unfortunately, not with the health of the new occupants. My advice to anyone suffering from mold illness is to find a well-constructed smaller home to rent, have it tested, and keep it dry! Happy house hunting!
References
- (n.d.). How Does Mold on Drywall in New Construction Happen? Affordable Remediation & Emergency Services. Retrieved July 22, 2024, from https://affordableremediation.com/mold-drywall-new-construction-happen/
- Lstiburek, J. (2009, November 11). BSI-027: Material View of Mold. Building Science.com Corporation. Retrieved July 22, 2024, from https://buildingscience.com/documents/insights/bsi-027-material-view-of-mold
- (n.d.). What is water absorption test of concrete? Explain in detail with test procedure and examples. The Engineer's Blog. Retrieved July 22, 2024, from https://engineersblog.net/what-is-water-absorption-test-of-concrete/
About the Author:
Brian Tinker recently joined Change the Air Foundation’s newly created Building Advisory Committee with the goal of protecting occupant health by changing the way we build our homes and buildings. Brian has been building custom homes in Colorado for the last 20 years.
During this time, he has seen many changes in building science, and oftentimes the changes within building codes have not been based on what's best for the people who live in the homes.
This issue became very real for Brian when his family discovered that his wife and son both had mold illness. Living in a 1931 house with plenty of water damage became an immediate concern. Tinker Homes had already begun changing the way they built to make homes healthier, but this new information rapidly accelerated the building science changes in his company. Brian is now working with several organizations and groups to increase awareness about building new homes with better building practices to improve the quality of the air inside buildings.