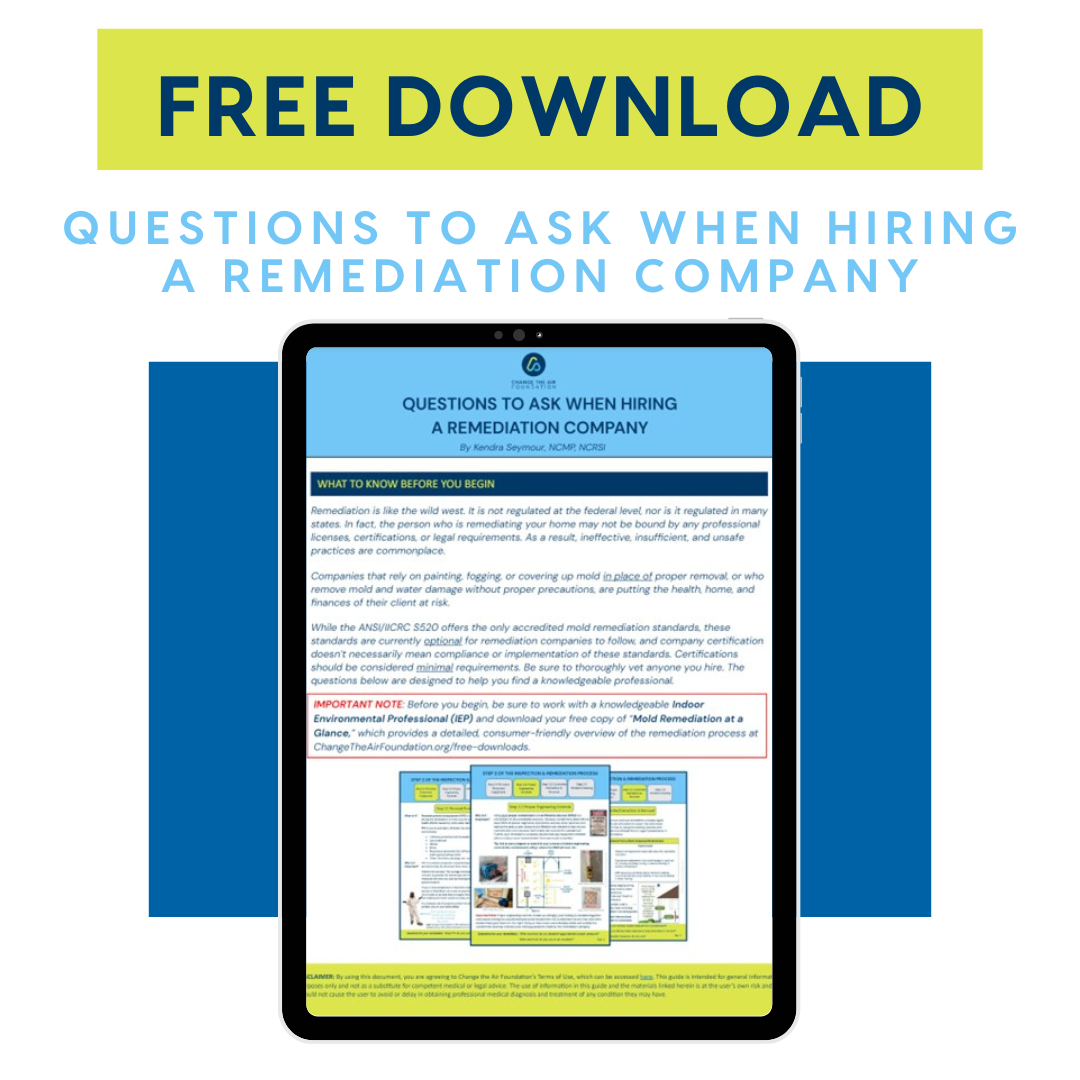
Questions to Ask When Hiring a Remediation Company
This helpful resource arms you with questions to ask about the remediation company’s certifications and insurance, remediation protocols, cross-contamination prevention measures, products used, methods of material disposal, and guarantees on their work.